VFD Training Course
Burraq Engineering Solutions is a company that offers a range of engineering services and solutions including VFD (Variable Frequency Drive) training courses. These courses are designed to teach individuals how to properly install, operate and maintain VFDs in industrial and commercial environments.
Training may include topics such as electrical theory, VFD components and operation, programming and troubleshooting, and safety procedures. The company may also offer other types of training such as PLC (programmable logic controller) training, motor control training, and other types of industrial automation courses. These courses typically cover topics such as electrical theory, VFD components and operation, programming and troubleshooting, and safety procedures. Upon completion of the course, individuals should have a thorough understanding of how a variable frequency drive works and how to properly use it in industrial and commercial environments.
VFD Training Course
Burraq Engineering Solutions is offering VFD training courses by a worldwide experienced actor. BES is offering physical classes of VFD training in Lahore and Online VFD training in all over Pakistan. For the last 8 years, we are serving in the field of Automation & Electrical Engineering, so all fresh graduates, and engineers. And professionals are invited to enhance their skills by joining our training sessions.
Burraq Engineering Solutions institute Provides the best IT and Engineering training in Lahore, Karachi, Faisalabad, Multan, Sahiwal, Islamabad, Hyderabad, Quetta, Peshawar, Rawalpindi, Gujranwala, Sialkot, Bahawalpur, Sahiwal, Rahim Yar Kahn, Dera Ghazi Khan, Dera Ismail Khan, Sheikhu Pura, and Mardan.
Great Offer
Our training program in the Gulf region is designed to empower individuals and organizations with the knowledge and skills they need to thrive in today’s dynamic and competitive landscape. We offer diverse training courses delivered by expert instructors with deep industry experience and a passion for sharing knowledge. Our curriculum covers various subjects, including leadership development, project management, communication skills, digital marketing, finance, technology, and Engineering Sector.
We offer in-person and online training options to cater to the preferences and availability of our participants. Our in-person training sessions provide an interactive and immersive learning experience, fostering collaboration and networking among participants. On the other hand, our online courses offer flexibility and convenience, allowing individuals to learn at their own pace from anywhere in the Gulf region like Kuwait, Dubai, Bahrain, Qatar, Saudi Arabia & Oman.
VFD Training Course Details
- Overview of different VFD’s, INVT, Danfoss and Schneider
- Selection of VFD for Motor
- Source of Freq.in VFD
- VFD of Operation in VFD
- Jog Mode of Operation in VFD
- Multiple Sources of Frequency in VFD
- Disable the Reverse Operation of Motor?
- How to Secure/Lock your Parameter?
- Multi-step Speed Commands in VFD
- Acceleration & Time & Speed Inhibit
- How to Bound the Frequency of Drive (Upper Bound & Lower Bound Function)
- How to Reset the External Fault in Drive
- How to change External Control of VFD
- VFD Operational Feedback (ON/OFF)
- Reading feedback of getting Desired Frequency in VFD
- VFD Biasing
- Biasing the Frequency
- Biasing the Frequency with Pot. Freq. Gain
- Biasing the Voltage
- Acc./Dec. Time 1 (Default)
- Acc./Dec. Time 2 (Conditional)
- Introduction to Scaling
- Wiring and Adulation of VFD
- Motor Sad Control using Built-in Potential.
- Motor Speed control using Katha pad of VFD
- Motor Speed control using 0-10V (Analog Values)
- Motor Speed control using 0-20mA (Analog Values)
- Motor Max and Min Frequency set/reset
- VFD Overload activation for Motor Protection
- Motor Reverse Forward using functions.
- Advance Functions
- Two Motors On/off using One VFD
- Motor Speed Control through Thermocouple (Analog Sensor)
- Motor Reverse Forward using external signals.
- Synchronization of two VFD’s (TEXTILE MILL Examples)
- Complete wiring of VFD
- Wiring of Analog sensors with VFD
Variable frequency drives or frequency converters are important elements in power electronics. They are used to convert an alternating voltage of a defined level and frequency into an alternating voltage of another or the same voltage level and frequency. Frequency converters are used to set the speed of AC and three-phase drives. By controlling the amplitude, frequency, and phase position of the voltage on the machine, it is possible to set the machine’s torque and speed.
The frequency converters are made up of a rectifier and an inverter and convert from AC to DC and back to AC. Their important role in practice means that they are viewed as a separate type of converter.
- Rectifier
- Inverter
- Intermediate circuit
The voltage supplied by the AC network is first rectified by the network-side rectifier, smoothed in the intermediate circuit and converted by the machine-side inverter into the voltage with the desired number of phases, frequency and amplitude
The line-side converter represents the link between the feeding network and the intermediate circuit (AC-DC). Depending on the design of the circuit, it is also an actuator for controlling the flow of energy. The AC-DC converter is implemented with an externally guided converter (rectifier).
The load-side converter sets the operating conditions required by the load, ie frequency, voltage, and current. It also represents an actuator for the flow of energy. This DC-AC converter can only be implemented with a self-commutated converter.
The intermediate circuit is responsible for the intermediate storage of the energy. This happens either as a direct voltage (voltage intermediate circuit or U converter) or as a direct current (current intermediate circuit or I converter). A capacitance or an inductance can serve as a memory. These are dimensioned in such a way that the voltage Us for the U converter and the current Id for the I converter are greatly smoothed and can be viewed as constant quantities. This decouples the two converters to such an extent that they can be controlled independently of one another.
- The most important advantage of a frequency converter is the possibility of Continuously changing the speed of a motor. The speed range can be significantly Expanded.
- A frequency converter enables the direction of rotation of a motor to be changed Quickly.
- Frequency converters absorb the peak start-up currents of a motor. Conventionally, various means were used for this, such as the star-delta connection, the starting Transformer or thermistor starter. This means that the supply network is not disturbed And the torque is not negatively influenced.
- A three-phase network is not always necessary in order to be able to use a frequency converter. For smaller motors there are single-phase frequency converters with 230 VAC input voltage. They then provide a three-phase AC voltage for motors at the output.
- Today’s frequency converters usually provide various interfaces. They allow a frequency converter to be controlled in different ways. This means that a frequency converter can usually be connected to a larger system without any problems. In addition to conventional control via terminals, interfaces such as Profibus or Profinet are widely used.
- Numerous parameters enable the drive to be optimally adapted to the requirements. These include, for example, up and down ramps, braking behavior or starting with an increased torque (voltage increase / boost).
- Numerous messages in the event of a malfunction make it much easier to localize the cause of the malfunction.
- There are frequency converters that are mounted both centrally (eg in a control cabinet) and decentrally (eg directly on a motor, wall mounting).
- Appropriate software is available for many frequency converters. This makes it possible to implement all settings, the entire commissioning, monitoring and troubleshooting via PC. The parameter values can be stored in a separate file and thus complete the documentation. 10. Different frequency converters are used depending on the area of application. Servo drives are used where, for example, very high speed, dynamics or positioning accuracy are required. They are used, for example, in industrial robots.
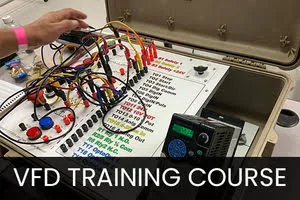
VFD training course
- Rs 22,000/-
- Course Duration 2 Months
- Online Session
- On Campus Lecture + Practical
- Video Lecture Available
- Urdu & English
- 24/7 Support